36 MM Very High Output Twin Screw Extruder
- New, modern design
- Maxi36Compounder output up to over 300 kg/hr
- With 55 and 90 kw Induction motors and also with 65 and 90 kw water cooled motors from Austria
- With high torque German made splined shafts
- With barrel linings and screw element in high wear resistant PM-HIP steel
With segmented screws on high torque splined shafts and closed barrel modules with PM-HIP steel linings & barrel lengths up to 60+ L/D and screw RPM of 900 for standard and 1200 for the Maxi36Compounder
New 36MM Twin Features
- Motor and Gearbox fully covered and with front and rear sliding doors equipped with a large poly-carbonate window with internal lighting for a clear view of the gearbox.
- Barrel sides covered by high polished stainless steel sections which can be easily removed to give room for additional side feeders and to inspect the barrel
- The top part of barrel cover with removable lids for easy addition of feed units, vent openings, etc.
This NEW very modern design of our Scientific 36 mm co-rotating twin-screw extruder is made with closed sectional barrel modules with inserted wear linings made from PM-HIP steel. In other words, the barrel is no longer of a clamshell type which we deemed not feasible for this larger twin. Each barrel module has a length of 4D, and the twin is available with many L/D sizes ranging from 40 to 60+.
The standard twin has a drive power of 55 kW AC induction motor or a 65 kW water-cooled motor and a max screw RPM of 900 as well as a re-designed high torque gearbox comprising of additional shaft supporting gears and a motor-driven gear pump closed-loop forced oil cooling system.
The NEW Maxi36Compounder is equipped with a 90 kW Induction Motor or water-cooled motor drive and same high torque gearbox having an additional shaft with supporting gears and a motor-driven gear pump for closed-loop forced oil cooling system. The max screw RPM with the Maxi Compounder is 1200 RPM as opposed to our standard versions where the max RPM is 900.
The water-cooled motors are of a new type from Austria which ensures a very efficient cooling and also minimize the size. An additional advantage with this motor type is that it has no fan and thus is not blowing air on to the body of the twin causing dust contaminations when running very dusty compounds.
All versions of our 36 mm twin screw extruder are equipped with High Torque splined screw shafts which give optimum strength to the shafts, withstanding with good margins the high torque from the motors. Also, the new oil cooling system for our high torque gearbox utilizes a block type of heat exchanger to ensure the gearbox is kept cold at even the severest running conditions. And the oil is circulated from a gear pump through a multitude of channels inside the gearbox to ensure that every moving part has very efficient lubrication.
The modular sectional barrel is as standard equipped with thick barrel lining inserts made from very high wear-resistant PM-HIP steel. This ensures a very long lifetime and it also allows for the compounding of very abrasive materials. Further, the twins can be supplied with the lining made from medium corrosion-resistant steel as well as very high corrosion-resistant versions made from M390 steel type from Germany. This latter steel type is useful for processing, for example of Fluor plastics and other resin types which develop aggressive acids during processing.
The screws are built up from individual elements mounted on the splined, hardened shafts. We have a large variety of screw feeding and kneading elements to enable optimum variations in screw configurations. These screw elements are also made from very high wear-resistant PM-HIP types of steel ensuring a longer lifetime as well as excellent resistance when producing compounds with abrasive ingredients. Also, we can offer two versions of acid-resistant elements where the highest resistant versions are made from M390 steel
Each barrel zone is equipped with both water cooling and electric cartridge heating, except for the infeed section which has only cooled. This allows for complete process control at each zone of the barrel and the water cooling coupled with the high wattage heating enables fast temperature changes of each zone when changing processing conditions from one compound to another. The water cooling is done from fine channels inside each barrel module and regulated with individual solenoid valves by its designated temperature controller.
We supply a screw extraction tool which makes it easy to remove the screws for cleaning etc.
The die is made with short distance to screws and minimum internal volume to enable very easy and fast cleaning. The die flange contains an easily removable breaker plate which can be exchanged with a distance ring, enabling production with or without screen packs.
The strand dies swings aside simply by loosening the two bolts to facilitate easy cleaning. For connection to other downstream equipment, such as flat die for a chill roll attachment, the extruder can optionally be supplied with a suitable die adaptor.
The extruders can optionally be equipped with a stainless steel volumetric hopper feeder with a single feed screw of spiral or solid screw types and with a stirring arm (agitator). This hopper feeder can optionally also be equipped with twin screws. The screw is driven by variable speed AC gear motor of 0.75kW power, and it has a digital screw speed control regulated on the touch screen.
The twins can optionally be equipped with one or more twin screw side feeders which are connected to the side of the barrel module. A special barrel module with opening as well as plug for side feeder is needed for this option, and the extruder can be supplied with several plugged side feeder modules for optimum flexibility of side feeder location. The new stainless steel barrel cover also has numerous removable cover plates for mounting of the side feeders. With this, it is also very easy to move the side feeder from one barrel zone to another. The side feeder has an infinitely variable speed drive with 36 mm diameter twin screws built up from the same elements as the main screws, and with an L/D ratio of 10. The barrel of the side feeder is as standard equipped with water cooling.
To fully utilize side feeders, it is recommended to use a system of gravimetric feeders where you can set an exact feed rate on all feeders to ensure an exact load of all ingredients.
The coupling in between the gearbox and drive motor is equipped with a torque limiter which will instantly disengage the coupling in the event that the screws are overloaded. The torque limiter is also equipped with a sensor which will stop the motor and a warning lamp on the control panel will indicate that the screws have been overloaded.
The extruder is equipped as standard with a computerized control system with large touch screen
Summary of Standard Features
- Extruder body is made in a very modern and streamlined design with the barrel section covered in stainless steel for easy cleaning and maintenance. Barrel cover has removable lids for side feeder making it easy to move feeder from one barrel zone to another
- The drive section of the twin with water-cooled motor and gearbox is enclosed and features a large acrylic window for visualization of the driving parts.
- 36 mm co-rotating segmented screws where each element can be placed anywhere on the splined screw shaft for optimum flexibility of screw configurations. A large variety of feed screws and needing elements will be available with similar designs to our smaller twins
- All screw elements are made with high wear-resistant PM-HIP steel, and they can also be supplied made from medium corrosion-resistant steel type SUS440C as well as with very high corrosion resistant M390 steel.
- Modular closed barrel sections with insert linings available with up to 60 L/D length (longer on request) and where each module has a length of 4 D.
- The modular section barrel is equipped as standard with a lining insert made from very high wear-resistant PM-HIP steel. This special steel also allows for high-temperature extrusions of up to 400 °C.
- All lining inserts are also available with medium corrosion-resistant steel type SUS440C and with Very High corrosion-resistant M390 steel.
- Water cooling as well as electric heating of each barrel module.
- High torque drives with a new oversized gearbox with forced and cooled oil lubrication for screw speeds up to 900 RPM for standard 36 mm twin and 1200 RPM for the Maxi36Compounder
- Motor power of 55 kW induction motor and 65 kW water-cooled motor for standard version as well as 90 kW Induction and water-cooled motor drive for the Maxi36Compounder.
- Stainless steel vent housing on the barrel equipped with sight glass and vacuum gauge as well as vacuum water ring pump with large stainless steel water tank. The barrel is also equipped with an atmospheric venting zone
- For the twins supplied with medium and high corrosion resistant steel types, the die is also made with corrosion-resistant steel. Further, all barrel modules for these versions are done in stainless steel
- Optionally the die flange can be equipped with an oval opening as well as oval-shaped breaker plate which allows for easier removal of the screws from the front, without removing the die flange.
- 250 bar pressure transducer at screw end, also equipped with a melt temperature sensor. Additionally melt sensors are placed on every second module, connected to digital temperature indicators on the control panel.
- Screws protected by a new sensitive torque limiter mounted in between the motor and gearbox.
Computerized PLC control with 10.4 inches full-color LCD touch screen
The computerized control has full visualization of all extruder parameters on the touch screen and is also offered with connection to an external PC where all data and programs can be downloaded. The high capacity PLC is supplied by B&R, Austria and the software is custom made by them exclusively for Labtech’ s twin-screw extruders. The controlling functions are as following:
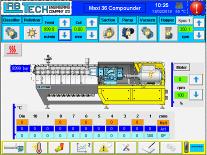
- Temperature up to 15 zones
- Motor speed with drive torque and RPM registration
- Pressure control of transducer at screw tip
- Speed control of hopper feeder as well as side feeders.
- Vacuum for barrel venting
- Pelletizer speed control, also control of optional variable speed strand feeding device
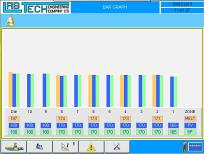
Alarm functions
- Main motor overload
- Hopper feeder overload
- Closed sectional barrel modules
- Overpressure on the die
- Low temp (on any zone) alarm if the present temperature is lower than the set temperature. This low-temperature alarm can be specified by operators.
- High temp (on any zone) alarm if the temperature is higher than the set temperature. This high temp alarm can be specified by operators.
- Pelletizer overload
- Strand feeding overload
Programs
The PLC can also store hundreds of preset programs with pre-selected running parameters of all extruder functions.
Four 36 MM Twin Versions
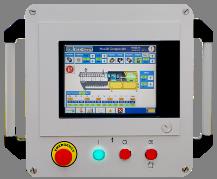
- The Maxi36Compounder with water-cooled 90 kW motor drive and max 1200 RPM
- The Maxi36Compounder with air-cooled 90 kW motor drive and max 1200 RPM
- The standard 36 Compounder with water-cooled 65 kW motor drive and max 900 RPM
- The standard 36 Compounder with air-cooled 55 kW motor drive and max 900 RPM
All versions utilize our new high torque gearbox with forced cooled oil lubrication and with our high torque splined screw shafts.
New Standard Features
- Both of our 36 mm twins are supplied with High Torque German-made splined screw shafts
- Both standard and the Maxi36Compounder have new closed barrel modules with heavy-duty wear linings in PM-HIP steel
- The 36 mm twins are also equipped with a new High Torque gearbox which has cooled and forced oil circulations from a gear pump.
- Both the standard 36 mm twin with 65 kW and the Maxi36 compounder with 90 kW motors are water-cooled featuring a compact design with a small footprint. The cooling water system enables very efficient cooling of the motor even at max load, and since it does not have any cooling fan, it eliminates any dust contaminations.
- New nice streamlined body design with everything covered, protecting internal components for dust and making the body very easy to keep clean.
Optional screw and barrel linings:
- Medium Corrosion Resistant screws and barrel linings to be used with low corrosion resin types such as PVC. Here the screw elements and barrel linings will be made in a stainless steel type SUS 440C
- Very High Corrosion Resistant screws and barrel inserts where the elements including screw shafts are made with M390 steel from Germany. This version is specifically designed for compounding of Fluor plastics and other high corrosive plastics. The M390 steel type offers a significant improvement in hardness and thus also wear resistance compared with earlier Inconel and Hastalloy types.
Maximum output on our 36 mm MaxiCompounder with 44 L/D and with a water-cooled drive of 90 kW. The tests were made running with virgin resins
Technical data for 36 mm Twin-screw extruders
Data
Data
Description
Standard
Maxi36 Compounder
Description
Standard
Maxi36 Compounder
Available L/D Ratio
40 to 60+ L/D
40 to 60+ L/D
Outer and inner screw diameter ratio (D/d)
1.63
1.63
Screw speed (RPM)
0 to 900
0 to 1200
Max barrel temp. (standard)
400 °C
400 °C
Motor Power (kW) Induction Motor
55 kW
90 kW
Heating power per barrel section(4 L/D)
3.2 kW
3.2 kW
Motor Power (kW) Water Cooled
65 kW
90 kW
Minimum water pressure and water consumption
3 bar/20lt/min
3 bar/20lt/min
Max. extrusion output pressure
250 bar
250 bar
Water pump power for optional closed-looped cooling system
0.75 kW
0.75 kW
Maximum torque at 900 RPM
2×340 Nm
2×340 Nm
Maximum output (with a medium to high density compound
150-200 kg/h
200-250 kg/h
Specific Torque Nm/cm3
13.53
13.53
Maximum output on our 36 mm MaxiCompounder with 44 L/D and with a water-cooled drive motor of 90 kW.
The tests were made producing of Masterbatches with high pigment loading
(The masterbatches were formulated and premixed by our customer, and thus the formulation is not fully disclosed. However, we know for sure that the mentioned pigment content and base resin is correct.)
Polymer Type (Regular Pellets)
Melt Flow Index (g/10min)
% of Maximum Motor Power
Screw (rpm)
Barrel temperature range ° C (starting from in feed zone)
MaxiCompounder Maximum Output
lb/hr
kg/hr
LDPE
20
87
1200
150 – 180
750
340
HDPE
15
70
1200
180 – 200
570
260
ABS*
18
70
1200
220 – 240
550
250
GPPS
8
75
1200
220 – 240
790
360
HIPS
8
75
1200
210 – 240
720
330
PP
11
80
1200
220 – 240
640
290
Masterbatch Type
Base Resin
Pigment content in %
Screw (rpm)
% of Max Motor Power
Maximum Output
Remarks
lb/hr
kg/hr
Phtalo Blue
LLDPE Powder + wax
40
1200
70
635
290
Masterbatch was premixed in High-Speed mixer
Phtalo Blue
LDPE Pellets + wax
40
1200
88
705
320
Same as above
White TiO2
LDPE Pellets
60
1200
65
705
320
Same as above
The tests were made with large quantities of pre-mixed masterbatches to ensure that the test results are correct.
The pre-mixed masterbatches were fed into main infeed port of the 36 mm twin screw extruder, using a volumetric single screw feeder with a spiral type of screw.
The twin was equipped with a 10-hole strand die with a hole diameter of 3 mm. The strands were led through our water bath type LW-300 And then pelletized in our high capacity pelletizer type LZ-200/VS.
This NEW very modern design of our Scientific 36 mm co-rotating twin-screw extruder is made with closed sectional barrel modules with inserted wear linings made from PM-HIP steel. In other words, the barrel is no longer of a clamshell type which we deemed not feasible for this larger twin. Each barrel module has a length of 4D, and the twin is available with many L/D sizes ranging from 40 to 60+.
The standard twin has a drive power of 55 kW AC induction motor or a 65 kW water-cooled motor and a max screw RPM of 900 as well as a re-designed high torque gearbox comprising of additional shaft supporting gears and a motor-driven gear pump closed-loop forced oil cooling system.
The NEW Maxi36Compounder is equipped with a 90 kW Induction Motor or water-cooled motor drive and same high torque gearbox having an additional shaft with supporting gears and a motor-driven gear pump for closed-loop forced oil cooling system. The max screw RPM with the Maxi Compounder is 1200 RPM as opposed to our standard versions where the max RPM is 900.
The water-cooled motors are of a new type from Austria which ensures a very efficient cooling and also minimize the size. An additional advantage with this motor type is that it has no fan and thus is not blowing air on to the body of the twin causing dust contaminations when running very dusty compounds.
All versions of our 36 mm twin screw extruder are equipped with High Torque splined screw shafts which give optimum strength to the shafts, withstanding with good margins the high torque from the motors. Also, the new oil cooling system for our high torque gearbox utilizes a block type of heat exchanger to ensure the gearbox is kept cold at even the severest running conditions. And the oil is circulated from a gear pump through a multitude of channels inside the gearbox to ensure that every moving part has very efficient lubrication.
The modular sectional barrel is as standard equipped with thick barrel lining inserts made from very high wear-resistant PM-HIP steel. This ensures a very long lifetime and it also allows for the compounding of very abrasive materials. Further, the twins can be supplied with the lining made from medium corrosion-resistant steel as well as very high corrosion-resistant versions made from M390 steel type from Germany. This latter steel type is useful for processing, for example of Fluor plastics and other resin types which develop aggressive acids during processing.
The screws are built up from individual elements mounted on the splined, hardened shafts. We have a large variety of screw feeding and kneading elements to enable optimum variations in screw configurations. These screw elements are also made from very high wear-resistant PM-HIP types of steel ensuring a longer lifetime as well as excellent resistance when producing compounds with abrasive ingredients. Also, we can offer two versions of acid-resistant elements where the highest resistant versions are made from M390 steel
Each barrel zone is equipped with both water cooling and electric cartridge heating, except for the infeed section which has only cooled. This allows for complete process control at each zone of the barrel and the water cooling coupled with the high wattage heating enables fast temperature changes of each zone when changing processing conditions from one compound to another. The water cooling is done from fine channels inside each barrel module and regulated with individual solenoid valves by its designated temperature controller.
We supply a screw extraction tool which makes it easy to remove the screws for cleaning etc.
The die is made with short distance to screws and minimum internal volume to enable very easy and fast cleaning. The die flange contains an easily removable breaker plate which can be exchanged with a distance ring, enabling production with or without screen packs.
The strand dies swings aside simply by loosening the two bolts to facilitate easy cleaning. For connection to other downstream equipment, such as flat die for a chill roll attachment, the extruder can optionally be supplied with a suitable die adaptor.
The extruders can optionally be equipped with a stainless steel volumetric hopper feeder with a single feed screw of spiral or solid screw types and with a stirring arm (agitator). This hopper feeder can optionally also be equipped with twin screws. The screw is driven by variable speed AC gear motor of 0.75kW power, and it has a digital screw speed control regulated on the touch screen.
The twins can optionally be equipped with one or more twin screw side feeders which are connected to the side of the barrel module. A special barrel module with opening as well as plug for side feeder is needed for this option, and the extruder can be supplied with several plugged side feeder modules for optimum flexibility of side feeder location. The new stainless steel barrel cover also has numerous removable cover plates for mounting of the side feeders. With this, it is also very easy to move the side feeder from one barrel zone to another. The side feeder has an infinitely variable speed drive with 36 mm diameter twin screws built up from the same elements as the main screws, and with an L/D ratio of 10. The barrel of the side feeder is as standard equipped with water cooling.
To fully utilize side feeders, it is recommended to use a system of gravimetric feeders where you can set an exact feed rate on all feeders to ensure an exact load of all ingredients.
The coupling in between the gearbox and drive motor is equipped with a torque limiter which will instantly disengage the coupling in the event that the screws are overloaded. The torque limiter is also equipped with a sensor which will stop the motor and a warning lamp on the control panel will indicate that the screws have been overloaded.
The extruder is equipped as standard with a computerized control system with large touch screen
Summary of Standard Features
- Extruder body is made in a very modern and streamlined design with the barrel section covered in stainless steel for easy cleaning and maintenance. Barrel cover has removable lids for side feeder making it easy to move feeder from one barrel zone to another
- The drive section of the twin with water-cooled motor and gearbox is enclosed and features a large acrylic window for visualization of the driving parts.
- 36 mm co-rotating segmented screws where each element can be placed anywhere on the splined screw shaft for optimum flexibility of screw configurations. A large variety of feed screws and needing elements will be available with similar designs to our smaller twins
- All screw elements are made with high wear-resistant PM-HIP steel, and they can also be supplied made from medium corrosion-resistant steel type SUS440C as well as with very high corrosion resistant M390 steel.
- Modular closed barrel sections with insert linings available with up to 60 L/D length (longer on request) and where each module has a length of 4 D.
- The modular section barrel is equipped as standard with a lining insert made from very high wear-resistant PM-HIP steel. This special steel also allows for high-temperature extrusions of up to 400 °C.
- All lining inserts are also available with medium corrosion-resistant steel type SUS440C and with Very High corrosion-resistant M390 steel.
- Water cooling as well as electric heating of each barrel module.
- High torque drives with a new oversized gearbox with forced and cooled oil lubrication for screw speeds up to 900 RPM for standard 36 mm twin and 1200 RPM for the Maxi36Compounder
- Motor power of 55 kW induction motor and 65 kW water-cooled motor for standard version as well as 90 kW Induction and water-cooled motor drive for the Maxi36Compounder.
- Stainless steel vent housing on the barrel equipped with sight glass and vacuum gauge as well as vacuum water ring pump with large stainless steel water tank. The barrel is also equipped with an atmospheric venting zone
- For the twins supplied with medium and high corrosion resistant steel types, the die is also made with corrosion-resistant steel. Further, all barrel modules for these versions are done in stainless steel
- Optionally the die flange can be equipped with an oval opening as well as oval-shaped breaker plate which allows for easier removal of the screws from the front, without removing the die flange.
- 250 bar pressure transducer at screw end, also equipped with a melt temperature sensor. Additionally melt sensors are placed on every second module, connected to digital temperature indicators on the control panel.
- Screws protected by a new sensitive torque limiter mounted in between the motor and gearbox.
Computerized PLC control with 10.4 inches full-color LCD touch screen
The computerized control has full visualization of all extruder parameters on the touch screen and is also offered with connection to an external PC where all data and programs can be downloaded. The high capacity PLC is supplied by B&R, Austria and the software is custom made by them exclusively for Labtech’ s twin-screw extruders. The controlling functions are as following:
- Temperature up to 15 zones
- Motor speed with drive torque and RPM registration
- Pressure control of transducer at screw tip
- Speed control of hopper feeder as well as side feeders.
- Vacuum for barrel venting
- Pelletizer speed control, also control of optional variable speed strand feeding device
Alarm functions
- Main motor overload
- Hopper feeder overload
- Closed sectional barrel modules
- Overpressure on the die
- Low temp (on any zone) alarm if the present temperature is lower than the set temperature. This low-temperature alarm can be specified by operators.
- High temp (on any zone) alarm if the temperature is higher than the set temperature. This high temp alarm can be specified by operators.
- Pelletizer overload
- Strand feeding overload
Programs
The PLC can also store hundreds of preset programs with pre-selected running parameters of all extruder functions.
Four 36 MM Twin Versions
- The Maxi36Compounder with water-cooled 90 kW motor drive and max 1200 RPM
- The Maxi36Compounder with air-cooled 90 kW motor drive and max 1200 RPM
- The standard 36 Compounder with water-cooled 65 kW motor drive and max 900 RPM
- The standard 36 Compounder with air-cooled 55 kW motor drive and max 900 RPM
All versions utilize our new high torque gearbox with forced cooled oil lubrication and with our high torque splined screw shafts.
New Standard Features
- Both of our 36 mm twins are supplied with High Torque German-made splined screw shafts
- Both standard and the Maxi36Compounder have new closed barrel modules with heavy-duty wear linings in PM-HIP steel
- The 36 mm twins are also equipped with a new High Torque gearbox which has cooled and forced oil circulations from a gear pump.
- Both the standard 36 mm twin with 65 kW and the Maxi36 compounder with 90 kW motors are water-cooled featuring a compact design with a small footprint. The cooling water system enables very efficient cooling of the motor even at max load, and since it does not have any cooling fan, it eliminates any dust contaminations.
- New nice streamlined body design with everything covered, protecting internal components for dust and making the body very easy to keep clean.
Optional screw and barrel linings:
- Medium Corrosion Resistant screws and barrel linings to be used with low corrosion resin types such as PVC. Here the screw elements and barrel linings will be made in a stainless steel type SUS 440C
- Very High Corrosion Resistant screws and barrel inserts where the elements including screw shafts are made with M390 steel from Germany. This version is specifically designed for compounding of Fluor plastics and other high corrosive plastics. The M390 steel type offers a significant improvement in hardness and thus also wear resistance compared with earlier Inconel and Hastalloy types.
Maximum output on our 36 mm MaxiCompounder with 44 L/D and with a water-cooled drive of 90 kW. The tests were made running with virgin resins
Technical data for 36 mm Twin-screw extruders
Data | Data | ||||
---|---|---|---|---|---|
Description | Standard | Maxi36 Compounder | Description | Standard | Maxi36 Compounder |
Available L/D Ratio | 40 to 60+ L/D | 40 to 60+ L/D | Outer and inner screw diameter ratio (D/d) | 1.63 | 1.63 |
Screw speed (RPM) | 0 to 900 | 0 to 1200 | Max barrel temp. (standard) | 400 °C | 400 °C |
Motor Power (kW) Induction Motor | 55 kW | 90 kW | Heating power per barrel section(4 L/D) | 3.2 kW | 3.2 kW |
Motor Power (kW) Water Cooled | 65 kW | 90 kW | Minimum water pressure and water consumption | 3 bar/20lt/min | 3 bar/20lt/min |
Max. extrusion output pressure | 250 bar | 250 bar | Water pump power for optional closed-looped cooling system | 0.75 kW | 0.75 kW |
Maximum torque at 900 RPM | 2×340 Nm | 2×340 Nm | Maximum output (with a medium to high density compound | 150-200 kg/h | 200-250 kg/h |
Specific Torque Nm/cm3 | 13.53 | 13.53 |
Maximum output on our 36 mm MaxiCompounder with 44 L/D and with a water-cooled drive motor of 90 kW.
The tests were made producing of Masterbatches with high pigment loading
(The masterbatches were formulated and premixed by our customer, and thus the formulation is not fully disclosed. However, we know for sure that the mentioned pigment content and base resin is correct.)
Polymer Type (Regular Pellets) | Melt Flow Index (g/10min) | % of Maximum Motor Power | Screw (rpm) | Barrel temperature range ° C (starting from in feed zone) | MaxiCompounder Maximum Output | |
---|---|---|---|---|---|---|
lb/hr | kg/hr | |||||
LDPE | 20 | 87 | 1200 | 150 – 180 | 750 | 340 |
HDPE | 15 | 70 | 1200 | 180 – 200 | 570 | 260 |
ABS* | 18 | 70 | 1200 | 220 – 240 | 550 | 250 |
GPPS | 8 | 75 | 1200 | 220 – 240 | 790 | 360 |
HIPS | 8 | 75 | 1200 | 210 – 240 | 720 | 330 |
PP | 11 | 80 | 1200 | 220 – 240 | 640 | 290 |
Masterbatch Type | Base Resin | Pigment content in % | Screw (rpm) | % of Max Motor Power | Maximum Output | Remarks | |
---|---|---|---|---|---|---|---|
lb/hr | kg/hr | ||||||
Phtalo Blue | LLDPE Powder + wax | 40 | 1200 | 70 | 635 | 290 | Masterbatch was premixed in High-Speed mixer |
Phtalo Blue | LDPE Pellets + wax | 40 | 1200 | 88 | 705 | 320 | Same as above |
White TiO2 | LDPE Pellets | 60 | 1200 | 65 | 705 | 320 | Same as above |
The tests were made with large quantities of pre-mixed masterbatches to ensure that the test results are correct.
The pre-mixed masterbatches were fed into main infeed port of the 36 mm twin screw extruder, using a volumetric single screw feeder with a spiral type of screw.
The twin was equipped with a 10-hole strand die with a hole diameter of 3 mm. The strands were led through our water bath type LW-300 And then pelletized in our high capacity pelletizer type LZ-200/VS.