Twin Screw Extruders: 12mm, 16mm, 20mm, 26mm (co & counter-rotating), 36mm models
with Modular Barrels for Maximum Temperature Control, and Easy Wear Replacement.
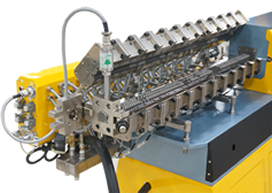
High Output 26mm. Maxi Compounder with 22 kW drive motor and 1200 max screw RPM
The Scientific 26 mm Combi co and counter-rotating twin screw extruder is made with a complete modular build up of the clam shell barrel, where each barrel section have a length of 4 D or 104 mm. The standard twin has a drive power of 15 KW and a max screw RPM of 400 for counter and 800 for Co-Rotating. It has a re-designed high torque 26mm COMBI twin screw with 15 KW drive and L/D of 40. New Counter rotating PVC screw Co-rotating screw for most thermoplastic resins gear box comprising of additional shaft supporting gears and a direct driven gear pump for closed loop forced oil lubrication and cooling. A pull-push mechanical gear selector will switch the screw rotation from co to counter rotation. It is located at the rear of the gearbox as shown here with the arrow. The 26 mm twin screw version is equipped as standard with splined screw shafts. The new oil cooling system for our high torque gear box utilizes a block type of heat exchanger to ensure the gear box is kept cold at even the severest running conditions. This also ensures optimum lubrication to all gears and bearings.
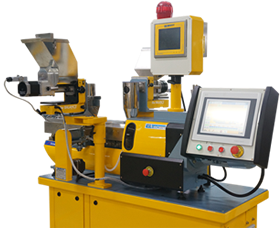
16mm twin screw with side feeders
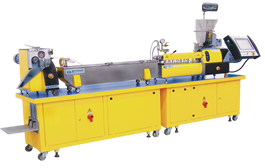
16mm twin screw table top strand compounding line
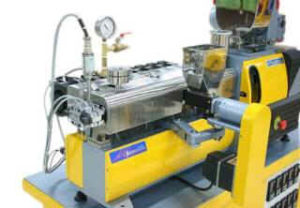
20mm twin screw with side feeder
Standard Features
- 26 mm Combi co and counter-rotating extruder barrel section is fully covered for safety propose and to protect from dust.
- 26 mm Combi co and counter-rotating segmented screws where each segment can be placed anywhere on the spline screw shaft for optimum flexibility of screw configurations. The kneading elements are supplied as single sectors which can be placed against each other in various angles enabling numerous kneading and shearing functions.
- All screw elements and barrel inserts are also available with high corrosion resistant steel type SUS440C and with very high wear resistant PPM types of steels
- Modular clam shell barrel with 40 L/D length and where each module has a length of 4 D. Barrel with balanced hinged top part for easy access to the screws.
- The modular Clam Shell Barrel is equipped as standard with exchangeable barrel lining insertsmade from a special high grade tool steel which have been through hardened to over 60 Rockwell C. This special steel also allows for high temperature extrusions of up to 400 °C.
- The standard screw and kneading elements are also made from high grade tool steel with through hardening and with a surface hardness of slightly below the hardness of the barrel inserts. Also the spline screw shafts are made of treated tool steel for optimum stiffness and high torque applications.
- Water cooling as well as electric heating of each barrel module.
- High torque drives with new oversized gear box having forced and cooled oil lubrication.
- Stainless steel vent housing on the barrel equipped with sight glass and vacuum gauge as well as vacuum pump protected with dual large filters coupled in series and mounted in sub cabinet of extruder.
- Variable speed single screw hopper feeder with stirring arm over the screws. Feeder components are equipped with quick locks for easy cleaning and the whole feeder assembly can easily be slid backwards for access to the extruder in-feed opening.
- Practical 4-holes strand die connected to extruder flange with 2 hinged bolts. The die is made with short distance to screws and minimum internal volume to enable very easy and fast cleaning. Also equipped with easy removable breaker plate in extruder flange, enabling production with or without a screen pack.
- Optionally the die flange can be equipped with oval opening as well as oval shaped breaker plate which allows for easier removal of the screws from the front, without removing the die flange.
- 300 bar pressure transducer at screw end, also equipped with melt temperature sensor. Additionally melt sensors are placed on every second module, connected to digital temperature indicators on the control panel.
- Screws protected by a new sensitive torque limiter mounted in between motor and gear box.
- Modern design with a sturdy sub cabinet containing all electric and electronic components in compartments completely separated from the vacuum pump assembly.
- Large clear vision control panel, mounted on a swing arm on the rear of the extruder and containing the following:
- One digital self tuning programmable temperature controller for each barrel module (10 units for the 40 L/D versions).
- Programmable pressure controller with digital indication of the screw tip pressure.
- Digital melt temperature indicators showing resin temperature at screw tip as well as at every second module. For the 32 L/D version there are then totally 4 melt temperature indicators and the 40 L/D versions have 5 of the same indicators.
- Digital RPM indicators for main screws speed as well as feeder screws speed with UP/DOWN scroll buttons to regulate speeds.
- Digital instrument showing screw torque in percent of max torque
- Clear warning lamps for:
-
- Over pressure at screw tip (depending on your individually set max pressure)
- Cooling water pressure too low
- Clam shell open
- Motor overload
- Torque limiter overload
- Feeder overload
- Temperature not reached set value on any of the controllers due for instance broken heating element